
This document defines the legal (contractual) relationship between the Uploader and the Administrator, as well as the legal (contractual) relationship between the User and the Uploader. TERMS OF USE OF THE WEBSITE SKRIWARE FOR UPLOADERS The part can be freely modified by following the link below:
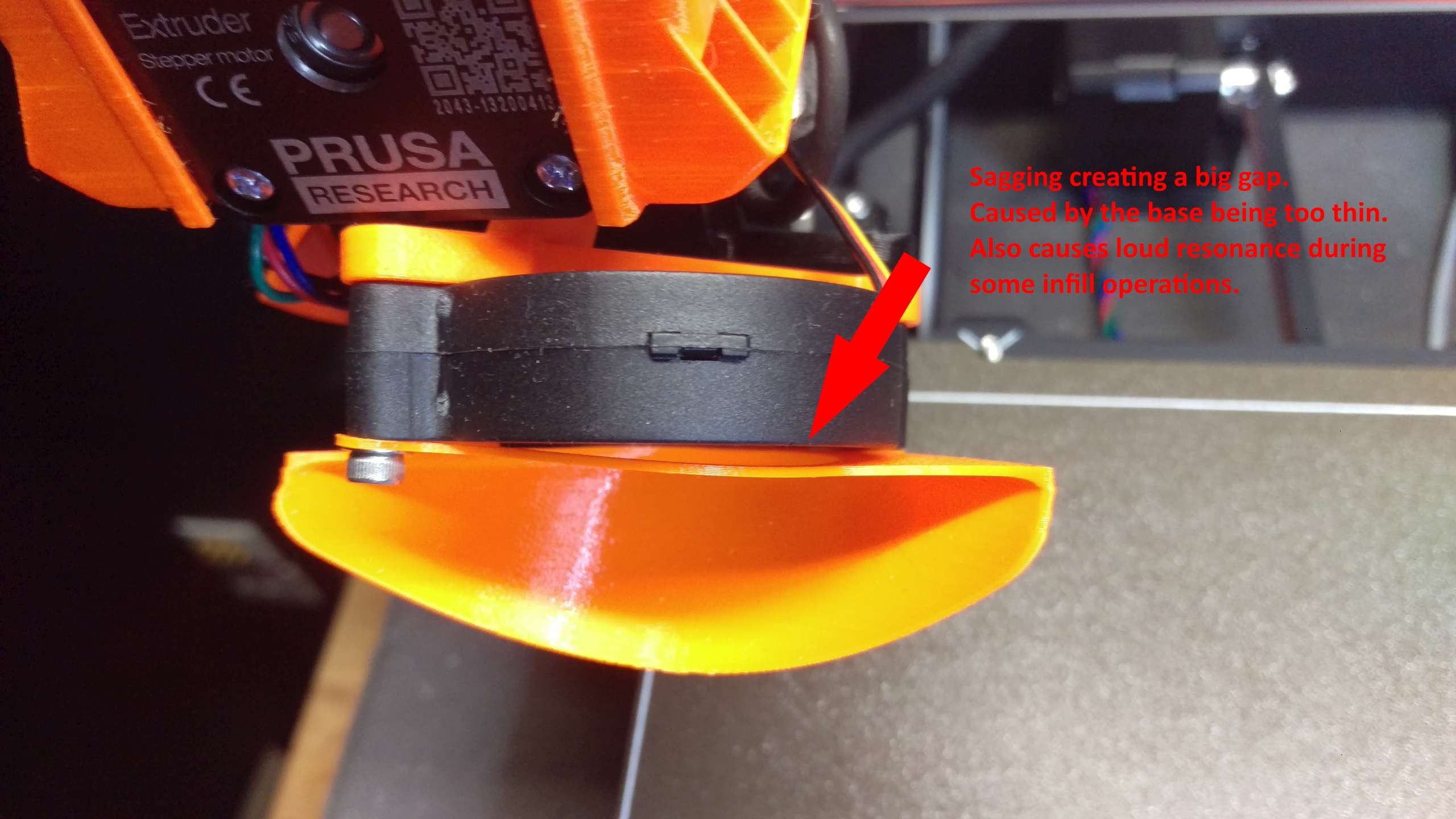
#Prusa fan shroud free#
Feel free to test it yourselves and share your findings with me. Bridging tests resulted in (marginally) less dangling and benchies printed mostly flawlessly for both fan shrouds, but were only slightly more stable on the front overhang with my fan shroud. Overall, my fan shroud did outperform the stock fan shroud in my testing, but not by an earth-shattering amount. That being said, this fan performed better than stock in most of my testing. In my testing, I found the limiting factor is mostly print settings and as long as the fan shroud does its job, the print quality can't be improved beyond what your slicer settings allow. The intention of this was to improve cooling rate on smaller prints. I combined this flow simulation testing with real world testing to determine if it meets my design goal. The goal with this design was to send as much air towards the tip of the nozzle as possible.
#Prusa fan shroud how to#
I learned how to set up flow simulations and used that to help me tune the performance of the fan duct. However, this fan duct works fairly well. My previous experiment, the 360 degree fan duct, didn't work out as well as I had hoped. If you print with polycarbonate regularly, we still suggest using glue stick to keep your satin sheet in the best shape possible.I've learned a lot from experimenting with different designs of fan duct.
#Prusa fan shroud Pc#
This surface doesn't need any separation layer if you print with PC Blend occasionally. This issue was moderated with the powder-coated satin sheet. If you print without a glue separation layer, you risk damaging the print sheet. PC Blend is printable on the powder-coated TXT sheet if you apply glue stick on it. Recommended nozzle and bed temperatures are 275☑0 ☌ and 110 ☑0 ☌. Prusament PC Blend is easy to print compared to other polycarbonates. This typically occurs with ambient temperatures below 18 ☌ when the printer cannot hold the high heatbed temperature. In some cases, the printer might show a “Bed thermal runaway” error. A lesser number of perimeters increases the chances of a successful print of large polycarbonate models. Denser infill (and more material inside the object in general) increases warping - and a risk of separation from the print surface. Warping is also affected by infill density and the number of perimeters. Prints with round edges warp less than those with sharp edges (this is true for any type of filament). Polycarbonate is not suitable for printing large objects covering the whole sheet. You should use the Brim function for printing parts with a small contact area with the print surface. This will make a microclimate with a slightly higher temperature around the model and increase your chances for a successful print. If you don’t have a printer enclosure, we suggest placing the object in the middle of the printing platform and setting the skirt value as high as possible. It is also possible to make your own enclosure. You can purchase the Original Prusa Enclosure in our e-shop. However, this is not recommended for large prints, where we recommend reducing this. For small to medium objects, you can increase infill to >25% and add more top layers (4 or more) for a stronger print.

Polycarbonate needs to be printed on a special surface, for example, a powder-coated sheet with a glue stick, PEI, or Build-tak. Printing polycarbonate is often tricky, as it tends to warp a lot, even with the additives. The best use of PC is for printing technical parts requiring great heat and mechanical resistance. ✖ Application of a separation layer is recommended ✖ High warping, especially with large models ✔ High impact tenacity and tensile strength ✖ Pure polycarbonate is highly hygroscopic
